铝合金产品加工的时候对精度要求非常的高,但是铝合金产品加工中难免会出现一些误差,那么铝合金产品加工都有哪些误差呢?下面我们就一起来了解一下吧! 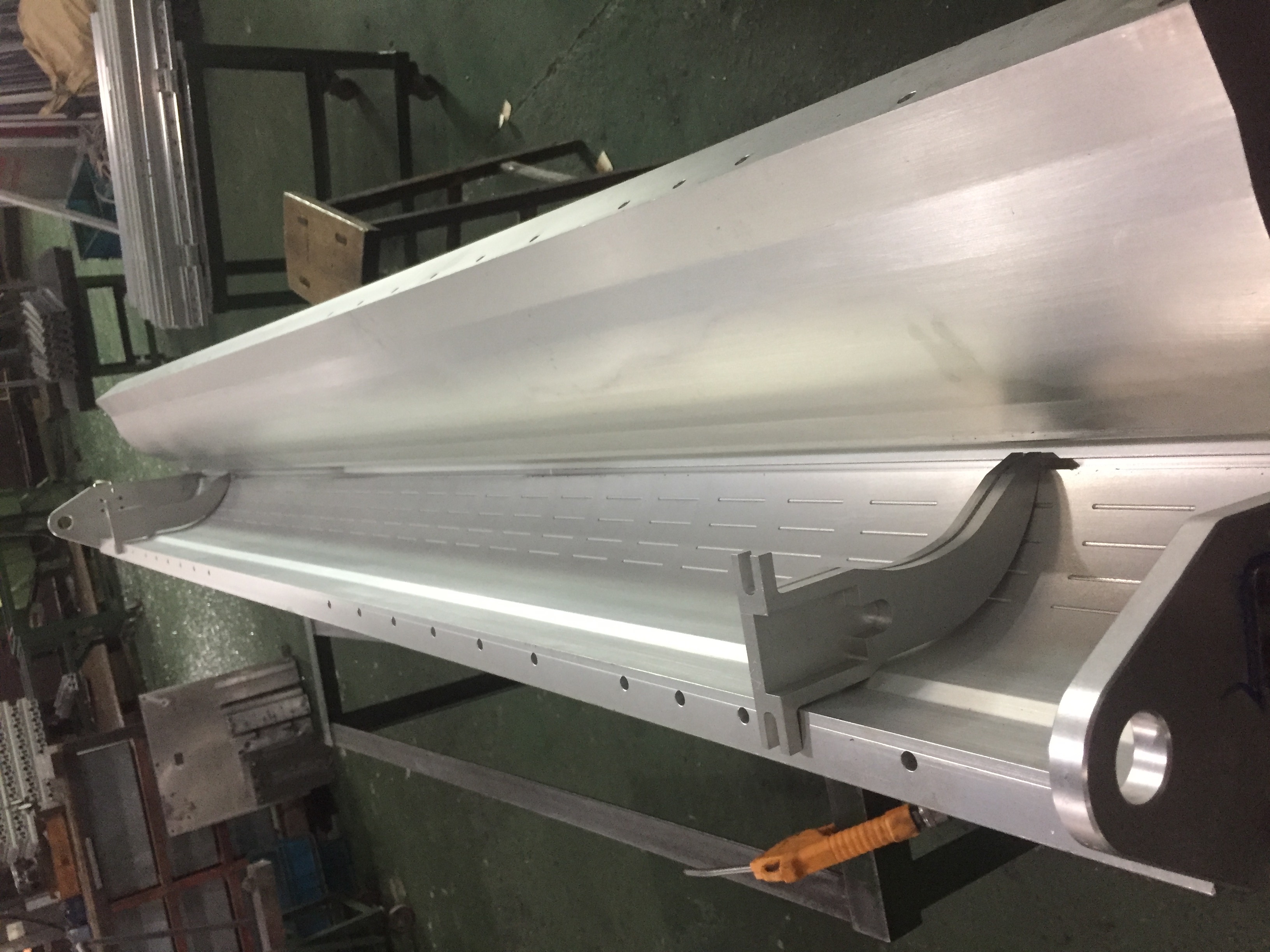
铝型材加工后实际几何参数与理想几何参数的吻合程度是铝型材的加工精度。加工误差越小,符合度越高,加工精度越高。铝型材的加工精度和加工误差是一个问题的两个方面。 铝型材加工误差的主要原因 一是机床制造误差 机床制造误差主要包括主轴回转误差、导轨误差和传动链误差。 二是夹具引起的误差 在铝型材加工中,夹具的作用是使工件等效于刀具和机床的正确位置,因此夹具的几何误差对加工误差(尤其是位置误差)有很大的影响。 第三,由工具引起的误差 任何刀具在切割过程中都会不可避免地磨损,从而导致铝型材的尺寸和形状发生变化。刀具几何误差对加工误差的影响因刀具类型的不同而有所不同:当使用固定尺寸刀具加工时,刀具的加工误差将直接影响铝型材零件的加工精度;对于一般刀具(如车刀),加工误差对加工误差没有直接影响。 四是定位误差 定位误差主要包括基准定位误差和定位分制造误差。在机床上加工铝型材时,必须选择工件上的几个几何要素作为加工的定位基准。如果使用选定的定位基准和设计依据(使用零件尺寸来确定表面的尺寸和位置)。基准测试)不一致,导致基线不匹配错误。 铝型材零件的定位面与夹具定位元件一起构成定位副。由于定位副的制造不准确以及定位副之间的匹配间隙导致工件的大位置变化,称为定位误差制造误差。定位误差和制造误差只有在使用调整方法时才会产生,不会在试切过程中发生。 五是工艺系统热变形 加工系统的热变形对加工误差有很大的影响。特别是在精密加工和长材料加工中,由热变形引起的加工误差有时可占到工件总误差的50%。 六是工艺系统受力变形 工件刚度:在加工系统中,如果工件刚度相对于机床、刀具、夹具较低,在切削力的作用下,由于铝型材刚度不足引起的变形对加工误差影响较大。 刀具刚度:外圆车刀在被加工表面法向(y)方向的刚度非常大,其变形可以忽略不计。内的内部直径较小的直径,杆的刚度很差,和杆的变形有很大的影响在孔的加工精度。 机床部件刚度:机床部件由多个部件组成。机床构件刚度没有合适的简单计算方法。目前,实验方法主要用于确定机床构件刚度。影响机床零件刚度的因素有:接头接触变形的影响、摩擦力的影响、低刚度零件的影响、间隙的影响。 7、调整误差 在铝型材加工的各个过程中,工艺系统总是以这样或那样的方式进行调整。由于调整不可能绝对准确,因此会产生调整误差。在加工系统中,通过调整机床、刀具、夹具或工件来保证工件与刀具在机床上的相互定位精度。当机床、刀具、夹具、铝件毛坯的原始精度满足工艺要求而不考虑动态因素时,调整误差对加工误差起决定性作用。 八、测量误差 当零件在加工过程中或加工后被测量时,测量方法、量具的精度、工件的精度以及主客观因素直接影响测量的精度。 九、内部压力 铝型材零件内部存在的应力。
通过上面铝合金产品加工厂家的介绍大家应该知道铝合金产品加工易产生的误差有哪些了吧!
更多铝合金产品加工相关资讯请访问官网:http://www.bmjmkj.com/